What Does GMP Certificate Means? Your Safety Guide
Discover what GMP certificate means, its role in ensuring product safety, and why it's essential for quality assurance. Learn more now!
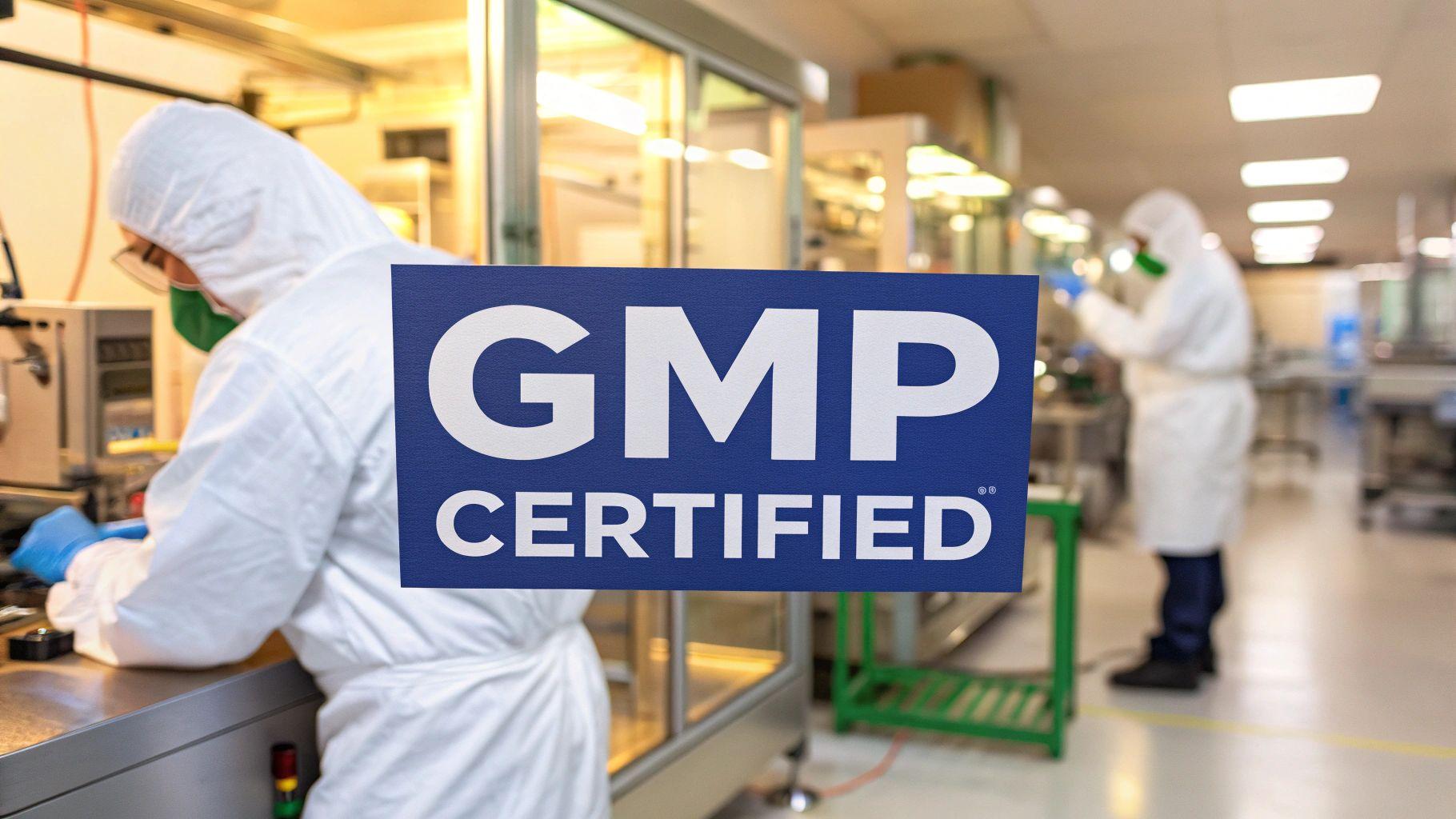
A GMP certificate is the official seal of approval showing a manufacturer sticks to strict quality standards, making sure their products are consistently safe, pure, and effective. You can think of it like a five-star rating for a factory. It verifies that every single step in the production process—from the moment raw materials arrive to the final sealed package—is obsessively controlled and documented.
In short, this certificate provides a rock-solid guarantee of quality and compliance.
What a GMP Certificate Really Guarantees
When you see a GMP certificate, it means so much more than a simple quality check. It’s a legally binding commitment to a system known as Good Manufacturing Practice (GMP). This system is designed to stamp out risks that can't be caught by just testing the final product, like contamination, incorrect labeling, or inconsistent potency.
Let's use an analogy. Picture a world-class restaurant kitchen. The head chef doesn't just taste the final dish and call it a day. They inspect every ingredient the moment it's delivered, enforce rigid hygiene rules for the staff, follow recipes down to the gram, and ensure every single plate that leaves the kitchen is a perfect copy of the last. A GMP certificate means a supplement factory operates with that same level of obsessive discipline and control.
The Foundation of Global Trust
This framework isn't some new industry trend. The Good Manufacturing Practice (GMP) certificate is a critical regulatory milestone that grew from guidelines first put together by the World Health Organization (WHO) way back in 1968. These standards require that all manufacturing processes are clearly defined, controlled, and documented, all while using proper facilities and well-trained staff.
Its importance became so universally recognized that by 2018, over 100 countries had woven WHO GMP provisions into their own national laws, creating a true global benchmark for safety and quality. You can dive deeper into the WHO's foundational role in GMP standards to see how it all started.
A GMP certificate transforms a company's promise of quality into a verifiable fact. It is the documented evidence that a manufacturer has built a robust system focused on producing safe and reliable products every single time.
The Pillars of GMP Certification
A GMP certificate isn't just about the finished product; it’s about the entire ecosystem that creates it. To earn one, a manufacturer has to prove they’ve mastered several key areas.
This table breaks down the core principles a facility must live by to get—and keep—their GMP certification.
Pillar | What It Means in Practice | Why It Matters |
---|---|---|
Process Control | Every step, from mixing to bottling, is validated and operates under strict controls to produce the same result every time. | Ensures consistency. The 100th bottle you buy is identical in quality and potency to the first. |
Contamination Prevention | Facilities are designed and maintained to prevent cross-contamination between different ingredients, batches, or finished products. | Guarantees purity. You get exactly what's on the label, with no unwanted or undeclared substances. |
Accurate Documentation | Every action is recorded—from receiving raw materials to shipping finished goods—creating a fully traceable production history for every batch. | Creates accountability and traceability. If there's ever a problem, the exact source can be pinpointed and fixed immediately. |
Personnel Competency | All employees are thoroughly trained for their specific roles and must follow strict hygiene and operational procedures. | Reduces human error. A well-trained team is the first line of defense against mistakes that could compromise quality. |
Ultimately, this comprehensive approach is what gives a GMP certificate its weight. It turns a simple piece of paper into a reliable indicator of a manufacturer's unshakable dedication to excellence.
Inside the 5 Pillars of Good Manufacturing Practice
When you see a GMP certificate, it means a manufacturer has mastered a system built on five core, interconnected pillars—what we in the industry call the '5 Ps'. These aren't just corporate buzzwords; they represent the exact areas an auditor digs into to verify a facility is truly committed to quality.
Think of it like building a house. You can't have a solid structure without a strong foundation, sturdy walls, and a protective roof. If any one of those fails, the whole house is compromised. It’s the same with GMP. This system ensures quality is built into the manufacturing environment from the ground up, not just checked at the end.
Let’s break down what each of these pillars looks like in the real world.
People and Premises
The first two pillars, People and Premises, lay the groundwork for a safe manufacturing environment. It all starts with the team. Every single person involved in making your supplements must go through rigorous, ongoing training on their specific job, strict hygiene protocols, and the company's standard operating procedures (SOPs). This means knowing exactly how to operate machinery and wearing the right protective gear to prevent any chance of contamination.
The facility itself is just as critical. The Premises have to be designed and maintained to eliminate any risk of cross-contamination. This involves creating logical workflows so materials move in a specific order, maintaining precise temperature and humidity levels, and using sophisticated air filtration systems. For instance, the United States Pharmacopeia (USP) specifies a controlled room temperature of 20°–25°C, with brief deviations only between 15°–30°C. This isn't just a suggestion—it's a hard rule that prevents sensitive ingredients from degrading.
Key Insight: A GMP-certified facility is a tightly controlled ecosystem. The synergy between highly trained people and a meticulously designed environment is the first line of defense against product defects.
Processes and Procedures
Next up are Processes and Procedures, which is where control becomes tangible and repeatable. Every single action, from the way raw ingredients are mixed to how bottles are filled and sealed, must follow a validated Process. This is how we guarantee that every batch is identical and meets the exact product specifications. If a formula requires a 10-minute mixing time, it has to be precisely 10 minutes, every single time. No exceptions.
This is where the real work happens, with technicians on the floor constantly monitoring equipment to ensure every process runs flawlessly.
The image above gives you a glimpse into this active, hands-on environment. It's far more than just a paperwork exercise.
But none of this works without the fifth pillar, Procedures, which is all about documentation. Every step, every measurement, every observation must be recorded in meticulous detail. This creates a complete, traceable history for each product batch, often called a "batch record." If a consumer ever reports an issue, the manufacturer can pull that record and trace the product's entire lifecycle to pinpoint the source of the problem and fix it. A simple mistake in documentation, like writing down the wrong lot number, could force a massive and incredibly expensive product recall.
Products: The Final Checkpoint
Finally, we have the Products pillar, which is all about the materials themselves. This covers two critical stages:
- Raw Materials: Before any ingredient is even allowed into the production area, it's held in quarantine. There, it's rigorously tested to confirm its identity, purity, and potency. Only after it passes these tests is it released for use in a formula.
- Finished Goods: Once the supplements are made and bottled, they aren't ready for sale just yet. The final products undergo another round of testing to confirm they meet all quality standards before being released to the market.
Together, these five pillars create a powerful, self-reinforcing system of checks and balances. A GMP certificate is proof that a manufacturer has mastered all of them, offering you a reliable guarantee of safety, consistency, and quality in every bottle.
What's the Difference Between GMP and cGMP?
When you're scanning a product label, you might spot "GMP" on one bottle and "cGMP" on another. They look almost identical, but that tiny "c" signals a massive commitment to quality. Understanding what a cGMP certificate really means can completely change how you choose your supplements.
So, what’s the big deal with the letter "c"? It stands for current. This one letter signals that a manufacturer isn’t just ticking the boxes for basic Good Manufacturing Practice standards. It means they are actively staying on top of the very latest industry advancements and technologies.
Think of it like the operating system on your phone. A five-year-old system (GMP) might technically still work, but it's slow and misses all the newest security patches and features. The latest version (cGMP), on the other hand, is constantly updated, giving you the best performance and protection against modern threats. A cGMP certificate is proof that a facility operates on that leading edge.
Proactive Quality vs. Reactive Compliance
At its core, the distinction is about being proactive with quality instead of just reacting to old rules. The core principles of GMP have been around since the mid-20th century, but cGMP forces a manufacturer to continuously evolve. Regulatory bodies like the FDA provide a framework, not a rigid, unchanging checklist. This pushes companies to adapt their systems with the newest tech and scientific insights. You can get a deeper dive into how cGMP reflects these ongoing advancements on ChromatographyOnline.com.
A company following basic GMP might just meet the foundational requirements set decades ago. But a cGMP-compliant manufacturer is always looking for what's next. They don’t just meet the standard; they raise it.
- Technology: Instead of relying on manual checks, they might use advanced, real-time sensors to constantly monitor and control crucial factors like temperature and humidity.
- Testing: They might adopt newer, more sensitive analytical methods for testing contaminants, allowing them to catch impurities that older techniques would have completely missed.
- Systems: They often use sophisticated software for documentation and traceability, which dramatically reduces the risk of human error and creates an airtight record.
cGMP is a dynamic promise. It’s a manufacturer's pledge that they aren't just following yesterday's rules but are actively integrating the most effective, up-to-date methods to guarantee product safety and quality.
Why cGMP Matters for You
As a consumer, this difference is huge. When you choose a product from a cGMP-certified facility, you’re getting an extra layer of confidence. It’s a clear sign that the company is at the forefront of quality control, investing in the best available tools and processes to protect your health.
In a fast-moving industry like supplement manufacturing, where new research and technologies are always emerging, this commitment to being current is what separates the good manufacturers from the truly great ones. It ensures the meaning of a quality certificate isn't stuck in the past but evolves right alongside science itself.
How a Manufacturer Earns a GMP Certificate
A GMP certificate isn't something a manufacturer can just buy off a shelf or get by filling out a form online. It has to be earned. This is a demanding, hands-on process that puts every single part of their operation under a microscope, and that rigorous journey is what gives the certificate its real authority.
Think of it like a surprise, top-to-bottom inspection from the world's toughest health inspector. The work starts long before an auditor ever shows up. A manufacturer first has to build a complete Quality Management System (QMS), which is essentially the master playbook for everything they do. This means painstakingly documenting every procedure, from how raw materials are tested when they arrive to the exact steps for cleaning a piece of machinery.
The Auditing Gauntlet
Once that robust system is built and followed day-in and day-out, the company can invite a regulatory body or a certified third-party auditor to start the official process. This kicks off the most critical phase: the on-site audit.
This isn't a friendly walkthrough. Auditors often arrive unannounced to get a genuine, unfiltered look at how the facility really runs. Their goal is to verify one crucial thing: that the documented procedures perfectly match the real-world practices on the factory floor.
During the audit, inspectors will:
- Review Records: They'll pour over batch records, training logs, maintenance reports, and cleaning schedules, looking for consistency and completeness.
- Interview Employees: They talk directly to people on the production line, asking them to explain their jobs to ensure training is not just done, but truly understood and applied.
- Inspect Equipment: They check that every machine is properly calibrated, maintained, and cleaned exactly as the procedures dictate.
- Observe Processes: They watch manufacturing happen in real-time, making sure every step is followed to the letter, every single time.
From Observation to Certification
After the audit, the inspectors issue a detailed report. It's almost unheard of for a facility to pass with a perfect score on the first try. More often, auditors will identify non-conformities or areas for improvement. These aren't just suggestions; they're mandatory fixes.
A GMP audit is designed to find and fix potential weaknesses before they can impact product quality. The certificate is only granted after the manufacturer proves they have corrected every single issue identified by the auditors.
The manufacturer then has to provide documented proof that all corrective actions have been put in place and are working. Only when the auditing body is completely satisfied that the facility meets every single standard is the GMP certificate finally awarded. It's this demanding, multi-stage process—from initial documentation to the final validation—that cements the trust and value behind every GMP seal. For brands looking to work with a proven partner, understanding the finer points of nutraceutical contract manufacturing is the first critical step.
How Global Agencies Enforce GMP Standards
A GMP certificate means very little if it isn’t backed by real, consistent enforcement. A piece of paper alone doesn’t guarantee quality; it’s the vigilant oversight of global regulatory agencies that does. These organizations are the guardians of Good Manufacturing Practice, ensuring that standards aren't just met for a one-time audit but are part of a facility's daily DNA.
Let’s use an analogy. Earning a driver's license (the certificate) is the first step, but it’s the traffic police (the agencies) who make sure you continue to drive safely on the road. In the world of supplements and pharmaceuticals, bodies like the Food and Drug Administration (FDA) in the US and the European Medicines Agency (EMA) are the ones patrolling the manufacturing highways.
Routine Inspections and Global Collaboration
The primary tool for enforcement? Routine inspections. These aren't just a formality; they are a major focus for regulatory bodies worldwide. The FDA, for instance, is known for conducting regular domestic GMP inspections that are typically unannounced, forcing facilities to stay compliant at all times. This state of constant readiness is essential, as any slip-up can lead to serious consequences. You can find out more about the foundational role of regulatory inspections on Wikipedia.
These agencies don’t operate in a vacuum, either. They collaborate on a global scale, sharing critical information about non-compliant manufacturers through databases like the EMA's EudraGMDP. This international network prevents a company that fails an inspection in one country from simply turning around and selling its subpar products in another.
The image below shows GMP guidelines from the European Union, illustrating the detailed framework agencies use to enforce these standards.
This table breaks down the specific chapters that cover everything from personnel to documentation, giving inspectors a clear, comprehensive checklist to work from during an audit.
The Consequences of Non-Compliance
When an agency finds violations, the penalties are severe and designed to protect public health above all else. They aren't just a slap on the wrist—they're structured to make cutting corners far more painful and costly than just following the rules in the first place.
Key Takeaway: The power of a GMP certificate comes from the real-world consequences of violating its standards. Enforcement transforms GMP from a set of guidelines into a legally binding requirement for safety and quality.
Consequences for failing to comply can escalate quickly and include:
- Warning Letters: Formal notices that demand immediate corrective action.
- Forced Product Recalls: Mandating the removal of unsafe or non-compliant products from the entire market.
- Hefty Fines: Significant financial penalties that can cripple a company's bottom line.
- Manufacturing Shutdowns: In the most serious cases, agencies have the authority to halt all production at a facility.
This robust, multi-layered enforcement network is what ensures a GMP certificate remains a trustworthy and meaningful symbol of quality. For entrepreneurs, understanding these high stakes is a crucial part of building a reputable brand, a foundational topic for anyone learning how to start a supplement business.
Why GMP Certification Matters When You Shop
So, what do all those technical standards and tough audits actually mean for you when you're standing in the aisle, looking at a bottle of supplements? It's simple, really. Seeing that GMP seal isn't just about a fancy logo; it’s your direct line to the quality control happening behind the scenes.
Think of it as a stamp of approval that turns complex manufacturing rules into a real-world promise you can rely on. A GMP certificate means the product in your hand comes with a powerful set of guarantees.
Confidence in Every Purchase
First and foremost, it guarantees safety. The GMP framework forces a manufacturer to have rock-solid systems in place to prevent contaminants, mix-ups, or impurities from ever making it into the final product. You can feel confident that what you’re taking is clean and pure.
Next, it gives you confidence in what you're buying. GMP ensures that what’s on the label is exactly what’s in the bottle—no more, no less. This kind of accuracy is non-negotiable for both effectiveness and safety, and you can dive deeper into these rules in our guide on dietary supplement labeling guidelines.
Finally, it delivers consistency. A GMP-certified process means the product you buy today will have the same quality, strength, and purity as the one you bought last month. That kind of repeatability is the true mark of a professional operation.
When you look for GMP certification, you're actively choosing a product that has been thoroughly vetted for quality, safety, and reliability. It’s a simple way to empower yourself and make smarter decisions for your health, all backed by a system built on excellence.
The difference between a certified and a non-certified product isn't always visible, but it's massive. Here’s a quick breakdown of what you're really choosing between.
GMP-Certified vs. Non-Certified Products: A Consumer's Guide
Feature | GMP-Certified Product | Non-Certified Product |
---|---|---|
Purity | Rigorously tested for contaminants, ensuring the product is clean and safe. | No guarantee of purity; may contain undeclared or harmful substances. |
Potency | The ingredient strength on the label is verified to be accurate in the bottle. | The actual dosage may differ significantly from what the label claims. |
Consistency | Each batch is manufactured under the exact same controlled conditions. | Product quality can vary wildly from one batch to the next. |
Ultimately, the choice is yours, but a GMP seal provides a level of assurance that unregulated products simply can't match. It’s about choosing peace of mind.
Your Top Questions About GMP Certification, Answered
When you're navigating the world of supplements, a lot of questions can pop up. It's totally normal. To help clear things up, we've put together answers to some of the most common questions we hear about GMP certification. This way, you can feel confident and informed about the products you choose.
Is a GMP Certificate a One-Time Award?
Not at all. Think of a GMP certificate less like a trophy you win once and more like a subscription you have to keep active. It’s not a permanent achievement.
Regulatory bodies and third-party auditors are constantly in the loop, conducting regular and often unannounced inspections. They’re there to make sure a manufacturer is upholding every single standard, day in and day out. If a facility slips up and fails a follow-up audit, its certification can be suspended or even revoked. This constant scrutiny is what ensures a GMP certificate means the same thing tomorrow as it does today: an unwavering commitment to quality.
Does GMP Certification Guarantee a Product Will Work for Me?
Here’s a crucial distinction: a GMP certificate guarantees the quality of the product, not your personal results. It’s your confirmation that the supplement was made in a clean, controlled environment and that it contains exactly what the label says it does—no more, no less, and with no contaminants.
However, it can't promise a specific health outcome. How a supplement works for you depends on a whole host of personal factors, like your unique body chemistry, diet, and lifestyle. A good way to think about it is this: GMP ensures the ingredients are pure and dosed correctly, which gives the product the best possible foundation to work as it's supposed to.
Key Insight: A GMP certificate is your assurance of the product's safety and integrity, not its specific effectiveness for your individual needs.
Can a Small or New Company Get a GMP Certificate?
Absolutely. GMP certification is all about the quality of a company’s processes and systems, not its size or how long it's been around. A small startup with a dedicated, compliant facility can earn a GMP certificate just as readily as a massive, established corporation.
The requirements are the same for everyone, big or small:
- A solid, well-thought-out Quality Management System (QMS).
- Detailed, meticulous documentation for every single step of every process.
- Strict adherence to all rules for hygiene, employee training, and operational controls.
As long as a company can prove it meets these tough standards during an audit, it can get certified. This really levels the playing field and allows new, quality-driven brands to compete with the big guys.
Ready to create a liquid supplement backed by the highest quality standards? Triton Nutra Group is your trusted cGMP-certified partner, turning your vision into a market-ready product with transparency and expertise. Launch your product with Triton Nutra Group.